Correctly shielding method
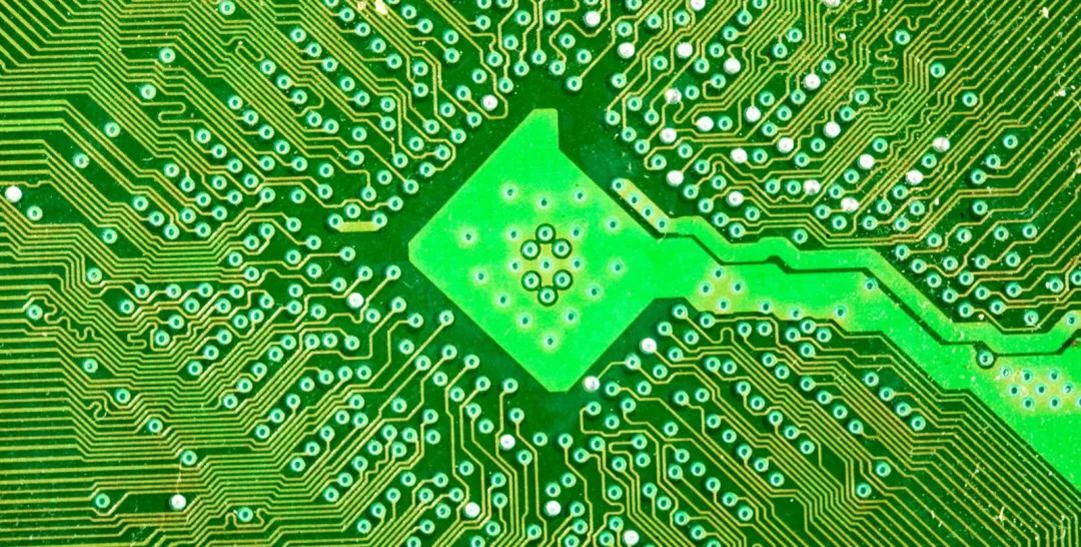
In product development, from the perspective of cost, progress, quality and performance, it is usually best to carefully consider and implement the correct design in the project development cycle as soon as possible. The functional solutions are usually not ideal in terms of additional components and other "fast" repair programs implemented in the later period of the project. Its quality and reliability are poor, and the cost of implementation earlier in the process is higher. The lack of foreseeability in the early design phase of the project usually leads to delayed delivery and may cause customers to be dissatisfied with the product. This problem applies to any design, whether it is simulation, numbers, electrical or mechanical.
Compared with some regions of blocking single IC and PCB, the cost of blocking the entire PCB is about 10 times, and the cost of blocking the entire product is 100 times. If you need to block the entire room or building, the cost is indeed an astronomical figure.
In product development, from the perspective of cost, progress, quality and performance, it is usually best to carefully consider and implement the correct design in the project development cycle as soon as possible. The functional solutions are usually not ideal in terms of additional components and other "fast" repair programs implemented in the later period of the project. Its quality and reliability are poor, and the cost of implementation earlier in the process is higher. The lack of foreseeability in the early design phase of the project usually leads to delayed delivery and may cause customers to be dissatisfied with the product. This problem applies to any design, whether it is simulation, numbers, electrical or mechanical.
Compared with some regions of blocking single IC and PCB, the cost of blocking the entire PCB is about 10 times, and the cost of blocking the entire product is 100 times. If you need to block the entire room or building, the cost is indeed an astronomical figure.
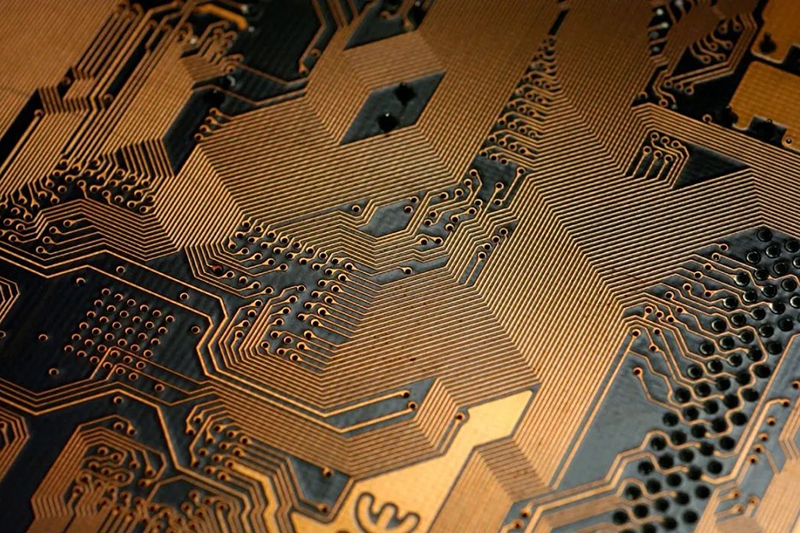
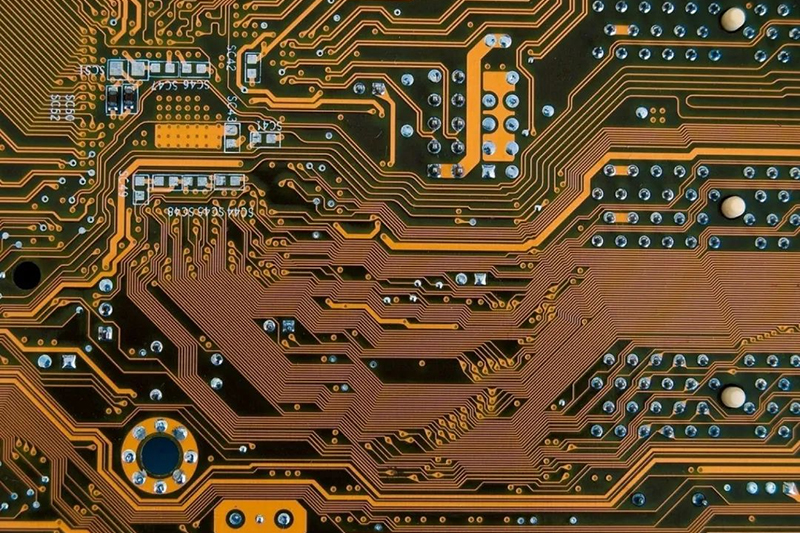
The target of EMI shielded is to create a Faraday cage around the closed RF noise components of the metal box. The five sides of the top are made of shielding cover or metal tank, and the side of the bottom is implemented with ground layers in PCB. In the ideal shell, no discharge will enter or leave the box. These shielded harmful emissions will occur, such as released from perforation to holes in tin cans, and these tin cans allow heat transfer during the return of solder. These leaks may also be caused by defects of EMI cushion or welded accessories. The noise may also be relieved from the space between the grounding of the ground floor to the ground layer.
Traditionally, the PCB shielding is connected to the PCB with a pore welding tail. The welding tail is manually welded manually after the main decoration process. This is a time -consuming and expensive process. If maintenance is required during installation and maintenance, it must be welded to enter the circuit and components under the shielding layer. In the PCB area containing a densely sensitive component, there is a very expensive risk of damage.
The typical attribute of the PCB liquid level shielding tank is as follows:
Small footprint;
Low -key configuration;
Two -piece design (fence and lid);
Pass or surface paste;
Multi -cavity pattern (isolate multiple components with the same shielding layer);
Almost unlimited design flexibility;
Vents;
Aable lid for fast maintenance components;
I / O hole
Connector incision;
RF absorber enhances shielding;
ESD protection with insulation pads;
Use the firm locking function between the frame and the lid to reliably prevent impact and vibration.
Typical shielding material
A variety of shielding materials can usually be used, including brass, nickel silver and stainless steel. The most common type is:
Small footprint;
Low -key configuration;
Two -piece design (fence and lid);
Pass or surface paste;
Multi -cavity pattern (isolate multiple components with the same shielding layer);
Almost unlimited design flexibility;
Vents;
Aable lid for fast maintenance components;
I / O hole
Connector incision;
RF absorber enhances shielding;
ESD protection with insulation pads;
Use the firm locking function between the frame and the lid to reliably prevent impact and vibration.
Generally, tin -plated steel is the best choice to block less than 100 MHz, while tin -plated copper is the best choice above 200 MHz. Tin plating can achieve the best welding efficiency. Because the aluminum itself does not have the characteristics of heat dissipation, it is not easy to weld to the ground layer, so it is usually not used for PCB level shielding.
According to the regulations of the final product, all materials used for shielding may need to meet the ROHS standard. In addition, if the product is used in a hot and humid environment, it may cause electrical corrosion and oxidation.
Post time: Apr-17-2023