【 Dry goods 】 In-depth analysis of SMT why to use red glue? (2023 Essence Edition), you deserve it!
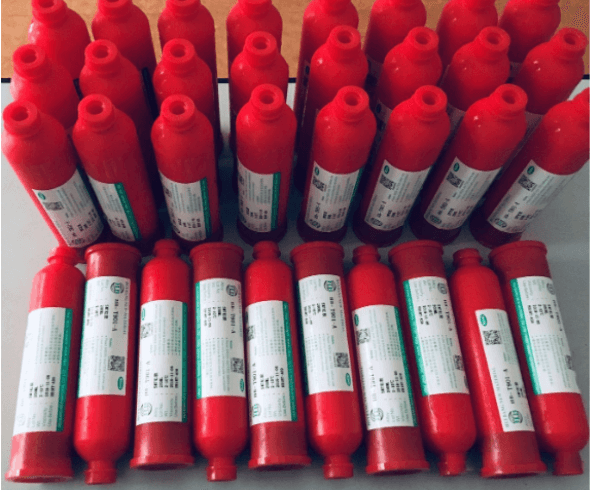
SMT adhesive, also known as SMT adhesive, SMT red adhesive, is usually a red (also yellow or white) paste evenly distributed with hardener, pigment, solvent and other adhesives, mainly used to fix components on the printing board, generally distributed by dispensing or steel screen printing methods. After affixing the components, place them in the oven or reflow furnace for heating and hardening. The difference between it and the solder paste is that it is cured after heat, its freezing point temperature is 150 ° C, and it will not dissolve after reheating, that is to say, the heat hardening process of the patch is irreversible. The use effect of SMT adhesive will vary due to the thermal curing conditions, the connected object, the equipment used, and the operating environment. The adhesive should be selected according to the printed circuit board assembly (PCBA, PCA) process.
Characteristics, application and prospect of SMT patch adhesive
SMT red glue is a kind of polymer compound, the main components are the base material (that is, the main high molecular material), filler, curing agent, other additives and so on. SMT red glue has viscosity fluidity, temperature characteristics, wetting characteristics and so on. According to this characteristic of red glue, in the production, the purpose of using red glue is to make the parts firmly stick to the surface of the PCB to prevent it from falling. Therefore, the patch adhesive is a pure consumption of non-essential process products, and now with the continuous improvement of PCA design and process, through hole reflow and double-sided reflow welding have been realized, and the PCA mounting process using the patch adhesive is showing a trend of less and less.
The purpose of using SMT adhesive
① Prevent components from falling off in wave soldering (wave soldering process). When using wave soldering, the components are fixed on the printed board to prevent the components from falling off when the printed board passes through the solder groove.
② Prevent the other side of the components from falling off in the reflow welding (double-sided reflow welding process). In the double-side reflow welding process, in order to prevent the large devices on the soldered side from falling off due to the heat melting of the solder, the SMT patch glue should be made.
③ Prevent the displacement and standing of components (reflow welding process, pre-coating process). Used in reflow welding processes and pre-coating processes to prevent displacement and riser during mounting.
④ Mark (wave soldering, reflow welding, pre-coating). In addition, when printed boards and components are changed in batches, patch adhesive is used for marking.
SMT adhesive is classified according to the mode of use
a) Scraping type: sizing is carried out through the printing and scraping mode of steel mesh. This method is the most widely used and can be used directly on the solder paste press. The steel mesh holes should be determined according to the type of parts, the performance of the substrate, the thickness and the size and shape of the holes. Its advantages are high speed, high efficiency and low cost.
b) Dispensing type: The glue is applied on the printed circuit board by dispensing equipment. Special dispensing equipment is required, and the cost is high. Dispensing equipment is the use of compressed air, the red glue through the special dispensing head to the substrate, the size of the glue point, how much, by the time, pressure tube diameter and other parameters to control, dispensing machine has a flexible function. For different parts, we can use different dispensing heads, set parameters to change, you can also change the shape and quantity of the glue point, in order to achieve the effect, the advantages are convenient, flexible and stable. The disadvantage is easy to have wire drawing and bubbles. We can adjust the operating parameters, speed, time, air pressure, and temperature to minimize these shortcomings.
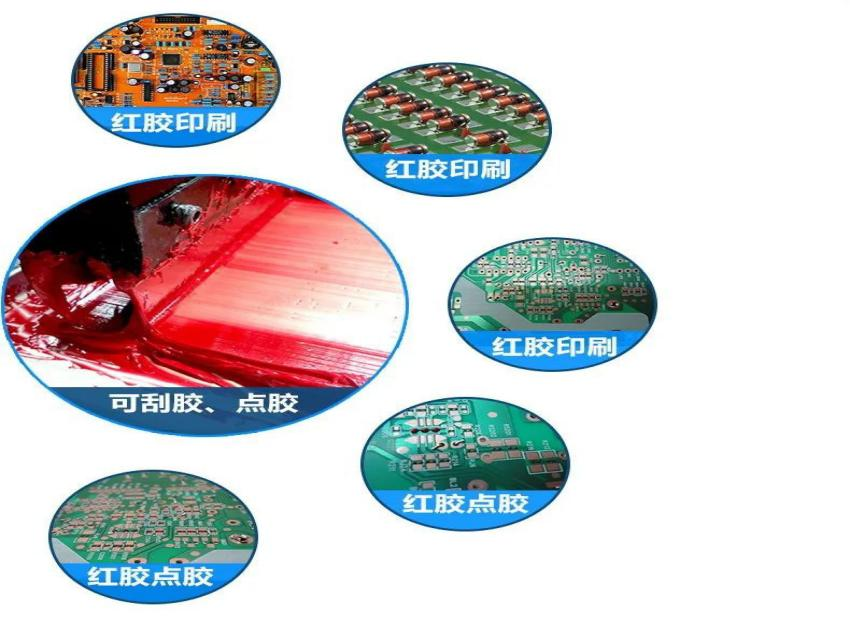
SMT patch adhesive typical curing conditions
Curing temperature | Curing time |
100℃ | 5 minutes |
120℃ | 150 seconds |
150℃ | 60 seconds |
Note:
1, the higher the curing temperature and the longer the curing time, the stronger the bonding strength.
2, because the temperature of the patch adhesive will change with the size of the substrate parts and the mounting position, we recommend to find the most suitable hardening conditions.
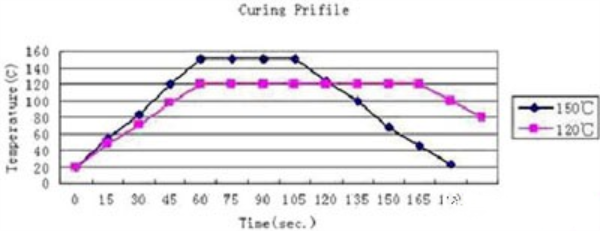
Storage of SMT patches
It can be stored for 7 days at room temperature, for more than 6 months at less than 5 ° C, and for more than 30 days at 5 ~ 25 ° C.
SMT adhesive management
Because SMT patch red glue is affected by temperature with its own viscosity, fluidity, wetting and other characteristics, so SMT patch red glue must have certain conditions of use and standardized management.
1) Red glue should have a specific flow number, according to the number of feed, date, type to number.
2) Red glue should be stored in the refrigerator at 2 ~ 8 ° C to prevent the characteristics from being affected due to temperature changes.
3) The red glue is required to be warmed at room temperature for 4 hours, in the order of first-in-first-out use.
4) For the dispensing operation, the red glue of the hose should be defrosted, and the red glue that has not been used up should be put back into the refrigerator for storage, and the old glue and the new glue can not be mixed.
5) To accurately fill in the return temperature record form, return temperature person and return temperature time, the user needs to confirm the completion of the return temperature before use. Generally, red glue cannot be used out of date.
Process characteristics of SMT patch adhesive
Connection strength: SMT adhesive must have a strong connection strength, after being hardened, even at the melting temperature of the solder does not peel.
Dot coating: At present, the distribution method of printed boards is mostly dot coating, so the glue is required to have the following properties:
① Adapt to various mounting processes
Easy to set the supply of each component
③ Simple to adapt to replace the component varieties
④ Stable dot coating amount
Adapt to high-speed machine: the patch adhesive now used must meet the high-speed of the spot coating and high-speed patch machine, specifically, that is, high-speed spot coating without wire drawing, and that is, high-speed mounting, printed board in the transmission process, the adhesive to ensure that the components do not move.
Wire drawing, collapse: once the patch glue sticks to the pad, the components can not achieve the electrical connection with the printed board, so the patch glue must be no wire drawing during coating, no collapse after coating, so as not to pollute the pad.
Low-temperature curing: When curing, the heat-resistant plug-in components welded with wave crest welding should also pass through the reflow welding furnace, so the hardening conditions must meet the low temperature and short time.
Self-adjustment: In the reflow welding and pre-coating process, the patch glue is cured and fixed before the solder melts, so it will prevent the component from sinking into the solder and self-adjustment. In response to this, manufacturers have developed a self-adjusting patch.
SMT adhesive common problems, defects and analysis
underthrust
The thrust strength requirement of the 0603 capacitor is 1.0KG, the resistance is 1.5KG, the thrust strength of the 0805 capacitor is 1.5KG, the resistance is 2.0KG, which can not reach the above thrust, indicating that the strength is not enough.
Generally caused by the following reasons:
1, the amount of glue is not enough.
2, the colloid is not 100% cured.
3, PCB board or components are contaminated.
4, the colloid itself is brittle, no strength.
Thixotropic instability
A 30ml syringe glue needs to be hit tens of thousands of times by air pressure to be used up, so the patch glue itself is required to have excellent thixotropy, otherwise it will cause instability of the glue point, too little glue, which will lead to insufficient strength, causing the components to fall off during wave soldering, on the contrary, the amount of glue is too much, especially for small components, easy to stick to the pad, preventing electrical connections.
Insufficient glue or leak point
Reasons and Countermeasures:
1, the printing board is not cleaned regularly, should be cleaned with ethanol every 8 hours.
2, the colloid has impurities.
3, the opening of the mesh board is unreasonable too small or the dispensing pressure is too small, the design of insufficient glue.
4, there are bubbles in the colloid.
5. If the dispensing head is blocked, the dispensing nozzle should be cleaned immediately.
6, the preheating temperature of the dispensing head is not enough, the temperature of the dispensing head should be set at 38℃.
wire-drawing
The so-called wire drawing is the phenomenon that the patch glue is not broken when dispensing, and the patch glue is connected in a filamentous way in the direction of the dispensing head. There are more wires, and the patch glue is covered on the printed pad, which will cause poor welding. Especially when the size is larger, this phenomenon is more likely to occur when the point coating mouth. The drawing of the patch glue is mainly affected by the drawing property of its main component resin and the setting of the point coating conditions.
1, increase the dispensing stroke, reduce the moving speed, but it will reduce your production beat.
2, the more low viscosity, high thixotropy of the material, the smaller the tendency to draw, so try to choose such a patch adhesive.
3, the temperature of the thermostat is slightly higher, forced to adjust to low viscosity, high thixotropic patch glue, then also consider the storage period of the patch glue and the pressure of the dispensing head.
caving
The fluidity of the patch will cause collapse. The common problem of collapse is that placing too long after the spot coating will cause collapse. If the patch glue is extended to the pad of the printed circuit board, it will cause poor welding. And the collapse of the patch adhesive for those components with relatively high pins, it does not touch the main body of the component, which will cause insufficient adhesion, so the collapse rate of the patch adhesive that is easy to collapse is difficult to predict, so the initial setting of its dot coating amount is also difficult. In view of this, we have to choose those that are not easy to collapse, that is, the patch that is relatively high in shake solution. For the collapse caused by placing too long after the spot coating, we can use a short time after the spot coating to complete the patch glue, curing to avoid.
Component offset
Component offset is an undesirable phenomenon that is easy to occur in high-speed SMT machines, and the main reasons are:
1, is the printed board high-speed movement of the X-Y direction caused by the offset, the patch adhesive coating area of small components prone to this phenomenon, the reason is that the adhesion is not caused by.
2, the amount of glue under the components is inconsistent (such as: the two glue points under the IC, one glue point is large and one glue point is small), the strength of the glue is unbalanced when it is heated and cured, and the end with less glue is easy to offset.
Over wave soldering off parts
The reasons are complex:
1. The adhesive force of the patch is not enough.
2. It has been impacted before wave soldering.
3. There is more residue on some components.
4, the colloid is not resistant to high temperature impact
Patch glue mix
Different manufacturers of patch glue in the chemical composition has a great difference, mixed use is easy to produce a lot of bad: 1, curing difficulty; 2, the adhesive relay is not enough; 3, over wave soldering off serious.
The solution is: thoroughly clean the mesh board, scraper, dispensing and other parts that are easy to cause mixing, and avoid mixing different brands of patch glue.